MATERIAL TECHNOLOGIES SOFTWARE
DIGIMU®

DIGIMU® proposes an industrial solution to mimic microstructural changes on a mesoscopic scale during metal forming processes.
DIGIMU® is the result of research projects conducted at the Central Research and Application Center for more than ten years, together with many industry stakeholders from the metallurgical, aerospace and nuclear sectors.
The full-field approach proposed by DIGIMU® has two main purposes:
DIGIMU® produces numerical polycrystalline microstructures that represent the heterogeneity of the material The boundary conditions applied to the REV represent the boundary conditions experienced by a point on the macroscopic scale (thermomechanical cycle of the desirable point)
Based on the Finite Element formulation, various physical phenomena that occur during metal forming processes are simulated (recrystallization, grain growth, dependent on second phase particles (Zener pinning, etc.).
DigitalClone for Engineering

The DC-E is a multibody system digital twin that uses physics-based models to make statistical life expectancy estimates of powertrain components. It is the only integrated solution in the world from system modeling, bearing and gear detailed analysis to simulation-based component life prediction. No solution other than DC-E includes microstructure-based lifespan predictions. Customers stated that thanks to their DigitalColone modeling, the iterations applied for design optimization can be reduced by 75% and the cost of part qualification can be reduced by up to 50%.
Our DC-E developer solution partner, Sentient Science, has more than 20 years of scientific research and development experience in increasing the lifespan of products, optimal testing and product design.
Build Your Own Models: Model systems and components, evaluate their lifespan Build your FMU (Functional Mockup Unit).
Component Lifetime Based on Fatigue: Estimation of component lifetime over the lifetime of the HMM software infrastructure.
Root Cause Analysis: Root cause analysis of early damages in your fleet can be carried out.
Model Management: Upload and manage working models to present your products on DigitalClone.
ADD VALUE
Risk analysis and design engineering applications of turbine and component technology in Renewable Wind Energy, Aviation and Railway.
Test new or proprietary materials that are not available in the database.
Conduct sensitivity studies to create a gold list of materials and optimally structure your assets.
DigitalClone for Additive Manufacturing
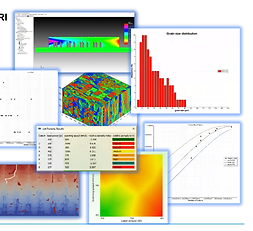
DC-AM is a physics-based Integrated Computational Materials Engineering platform developed for additive manufacturing parts that models process-microstructure-fatigue performance in conjunction. The solution virtually analyzes additive manufacturing parts at the micro scale, including grain size, grain morphology, porosity. Customers stated that thanks to their DigitalColone modeling, the iterations applied for design optimization can be reduced by 75% and the cost of part qualification can be reduced by up to 50%.
Three main steps are used in DC-AM to predict the life of the part and to analyze whether it is working with the most suitable parameters.
Process Modeling: Residual stresses and strains related to process parameters.
Microstructure Modeling: Grain structure and porosity depending on the location and parameters studied.
Fatigue Modeling: Fatigue performance under certain loading conditions.
The physics-based simulation package has been used in different additive manufacturing platforms (PBF, DED) and various alloy systems that our customers are working with. Related materials are Inconel 625, Inconel 718, 7-4 PH, 15-5 PH stainless steel, Ti64 and AlSi10Mg alloys. Apart from that, simulation can be applied to new alloys with minimal calibrations required.
ADD VALUE
DC-AM is a physics-based Integrated Computational Materials Engineering platform developed for additive manufacturing parts that models process-microstructure-fatigue performance in conjunction.
A unique microstructure module is available that virtually examines Additive Manufacturing parts at the microscale, including grain size, grain morphology, and porosity.
It includes a proprietary fatigue modulus that estimates fatigue performance taking into account microstructural defects and variations.
It is a cloud-based software that takes advantage of AWS (Amazon Web Service) high-performance processing power for fast simulation.
ThermoCalc
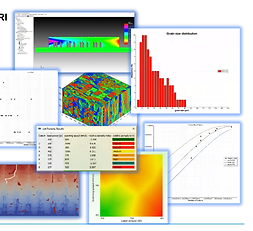
All calculations within Thermo-Calc are made using the thermodynamic databases within Thermo-Calc. Thermo-Calc offers its users a wide selection of high-quality databases containing materials of many different structures for different types of calculations.
The database sets within Thermo-Calc have been created by material engineers, who are experts in their fields, based on the CALPHAD technique, as a result of comprehensive scientific research and systematic evaluation of experimental and theoretical data.
Calculations of stable and metastable heterogeneous phase equations
Phase ratios and % composition amounts
Thermochemical calculations such as enthalpy, thermal capacity and thermal conversions
Transformation temperatures: liquefaction – solidification
Major parameters causing phase transformations
Phase diagrams (containing binary, triple and multiple components)
Application of solidification calculations to Scheil-Gulliver material models
Thermodynamic properties of chemical reactions
And many more are used in thermochemical calculations.